Fabrication.
Fabrication Expertise.
A&P Group has a long-standing history of delivering complex and technically-challenging oil and gas, renewable and marine infrastructure projects from its UK facilities, many of which call on the group’s longstanding fabrication expertise.
Fabrication expertise spans subsea and floating structures, topsides, foundation structures, pressure vessels, substations and wave and tidal devices. The team also has significant expertise in the fabrication, pre-commissioning and direct load-out of modularised offshore structures. Using in-house capabilities to maintain tight project control, we offer the complete integrated package from structural, piping and mechanical, through to E&I work.
With a highly skilled workforce including naval architects, designers and specialist fabricators as well as extensive, well-equipped facilities across the UK, A&P Group has an unfaltering commitment to quality driven engineering excellence.
Projects.
A&P Group’s most high-profile fabrication projects include building subsea structures for the UK North Sea sector as well as fabrication of blocks for the new Queen Elizabeth Class aircraft carrier, the Astute Submarine class and more recently the aft end of the new RRS Sir David Attenborough polar explorer vessel.
Projects.
Plant and Equipment
Our fabrication halls are equipped with an outstanding choice of fixed machines, large areas for assembling panels, blocks, modules and sub-assemblies, plus many overhead cranes of various capacities.
Main Fabrication Hall
- 6,750 square metre’s dedicated to three-dimensional fabrication
- 130 tonne hydraulic trailer
- Crane lifts to 100 tonnes
- Door size 19.5 x 12.8 metres
Full Fabrication Facility Spec
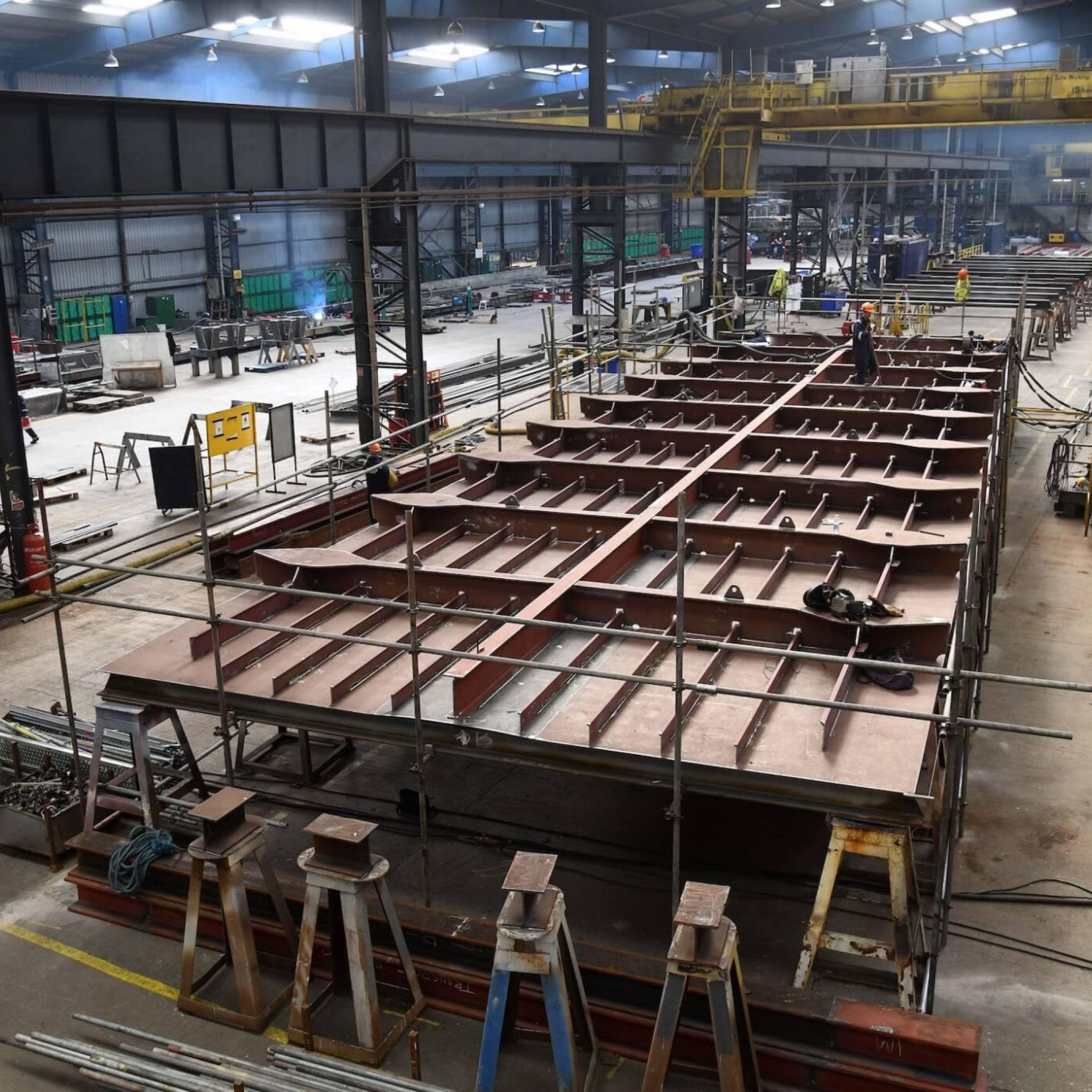