Block Build.
Type 26
A&P and Cammell Laird have been awarded contracts by BAE Systems to build units for the Royal Navy’s Type 26 Frigates.
A&P Tyne - which boasts the largest fabrication facilities on the east coast of England - has built four lower units for Ship No3, HMS Belfast, all of which were delivered earlier this year. Cammell Laird - which operates one of the largest construction halls in Europe - is building units for Ship 4, it will also be joining all of these units together.
Ian Douglas, Managing Director at A&P Tyne said: “A&P Tyne has completed block build units for some of the most significant ship building projects in recent time – including the Queen Elizabeth Aircraft Carriers, the RRS Sir David Attenborough and units for both the Astute and Dreadnought class submarines.
“A&P Tyne is delighted to have delivered units for Ship No3, HMS Belfast, of the Type 26 frigates and build on our collaboration with BAE Systems.
“We are also proud to be supporting our colleagues at Cammell Laird by sharing vital experience and knowledge from the build of Ship 3. This vital knowledge has added significant efficiencies to Cammell Laird’s delivery of units for Ship No4, HMS Birmingham.”
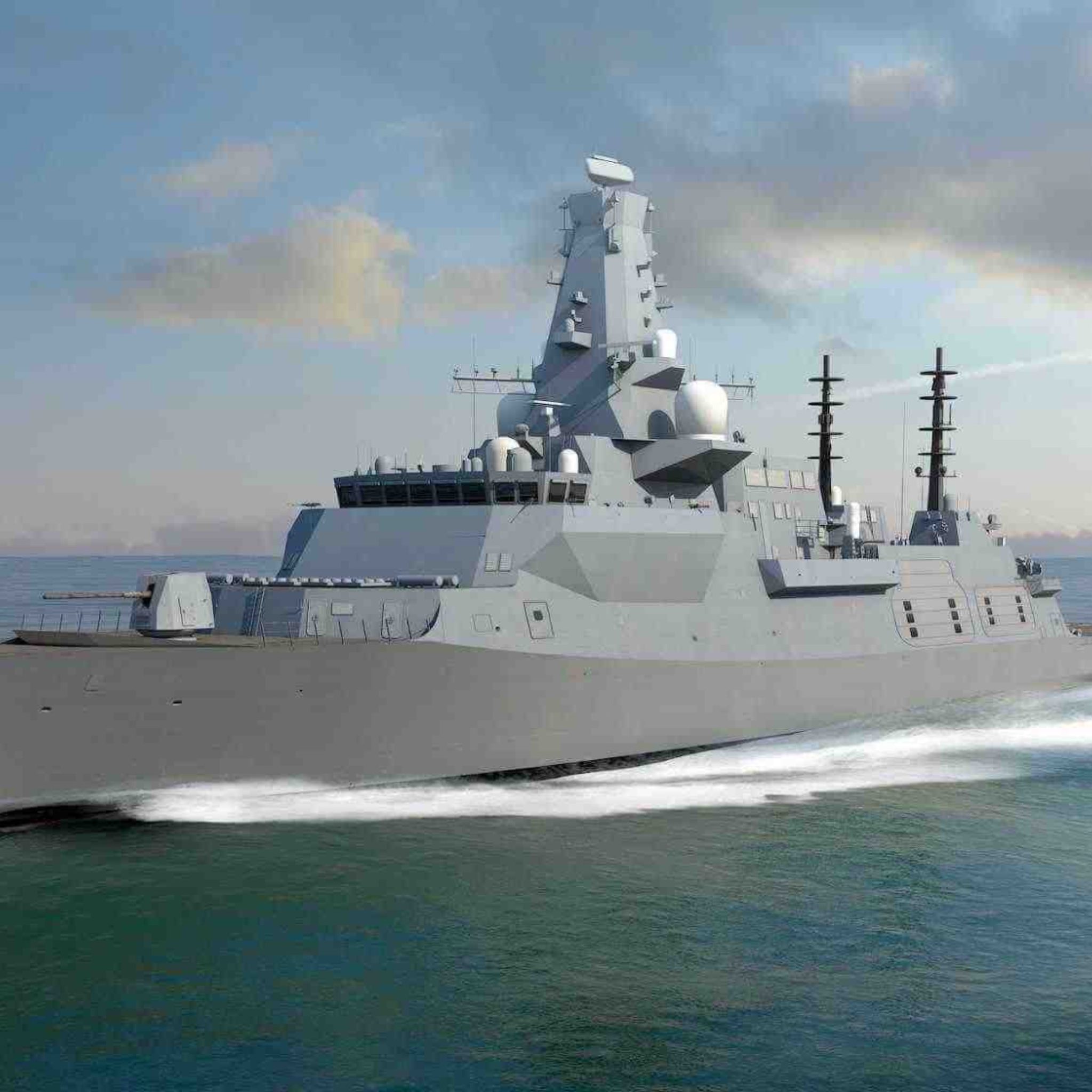
RRS Sir David Attenborough.
A&P Tyne’s specialist team of engineers and fabricators has invested more than 175,000 man hours in the fabrication of the 899-tonne steel stern, also known as Block 10, which is the equivalent weight of 71 London double decker buses and more than 23 meters long and 24 meters wide.
The stern formed part of the new ship RRS Sir David Attenborough, which is a major UK Government investment in frontier science. Commissioned by NERC, and built by marine engineering company Cammell Laird Shiprepairers & Shipbuilders Ltd, the vessel is a Rolls-Royce design and will be operated by British Antarctic Survey when the ship enters service in 2019.
The aft end left A&P Tyne in Hebburn for Cammell Laird, where the vessel was completed.
David McGinley, CEO of A&P Group, said: “This project is the very epitome of how the UK’s ship building industry can work together to not only deliver the best in class engineering and fabrication but to hone and nurture the very best talent and skills too.
“As one of the country’s leading fabrication businesses we’ve been actively involved in many major projects for the commercial marine, defence, oil and gas, subsea and offshore wind sectors and it’s a privilege and honour to add such a high profile and important research ship to the list. This project is also testament that ship building continues to flourish on the Tyne.”
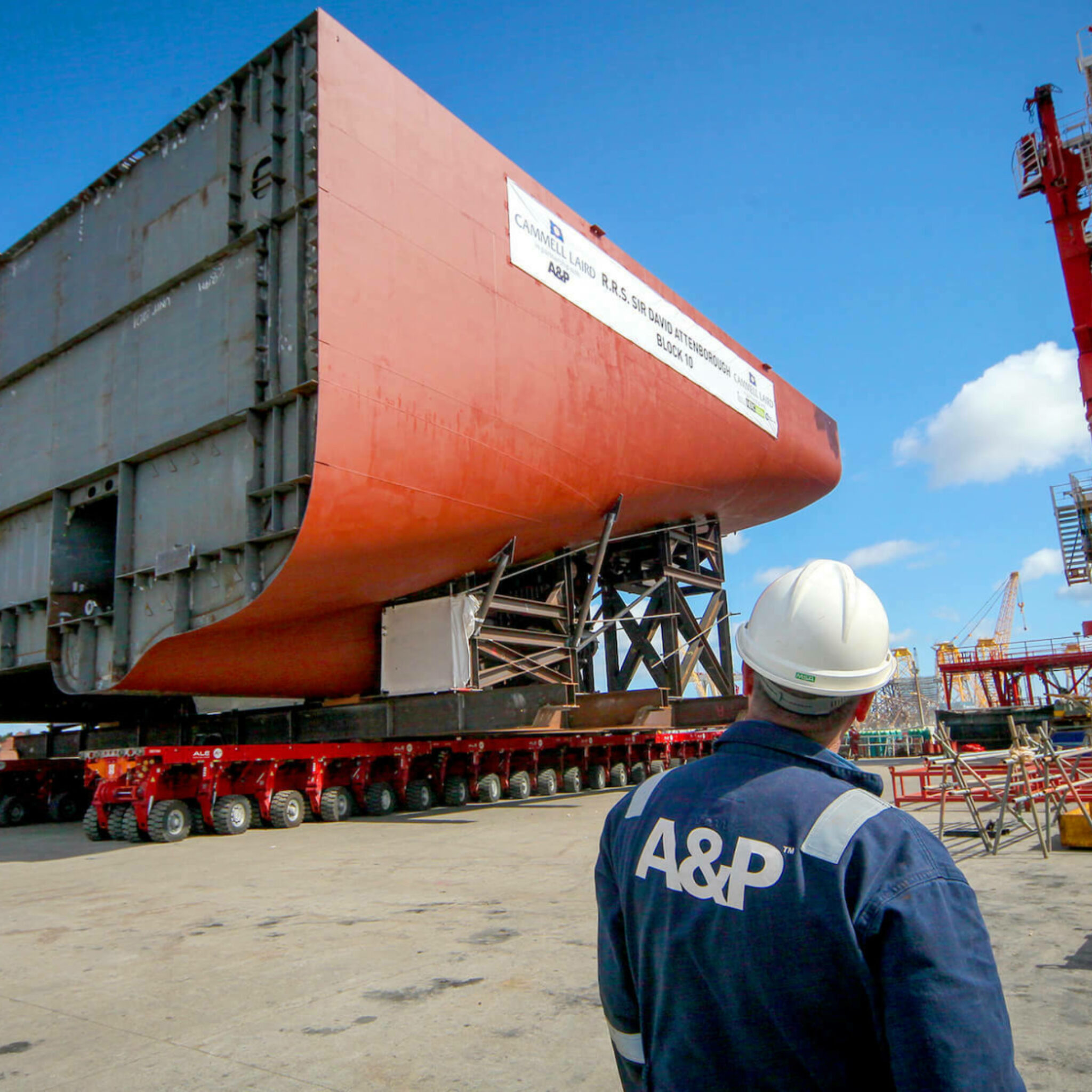
Aircraft Carriers.
Working as part of a consortium of British suppliers, A&P Group delivered two separate contracts ahead of schedule for both ships, HMS Queen Elizabeth and HMS Prince of Wales – the largest warships ever constructed for the Royal Navy.
A highly skilled team of 30 project personnel, 33 operations personnel and 500 engineering specialists made up of pipeworkers, engineers, welders, fabricators, electricians, sheet metal workers and painters as well as whole ship contractors delivered the programme over a four-year period.
The contracts covered the fabrication of double bottom units for the main blocks for BAE Portsmouth and the construction of the upper blocks for BAE Clyde, which form part of the vessels’ flight deck and hangars.
A&P’s preparation for the project was extensive. As well as building a new load-out quay, A&P also invested in a new panel line, burning machines, kempi ‘snake’ welding technology and heat straightening equipment.
This was a complex and intensive fabrication project from star to finish, rounded off with a high-stakes loud out, all of which was executed to the very highest quality standards, ahead of schedule.
Both vessels are now in service.
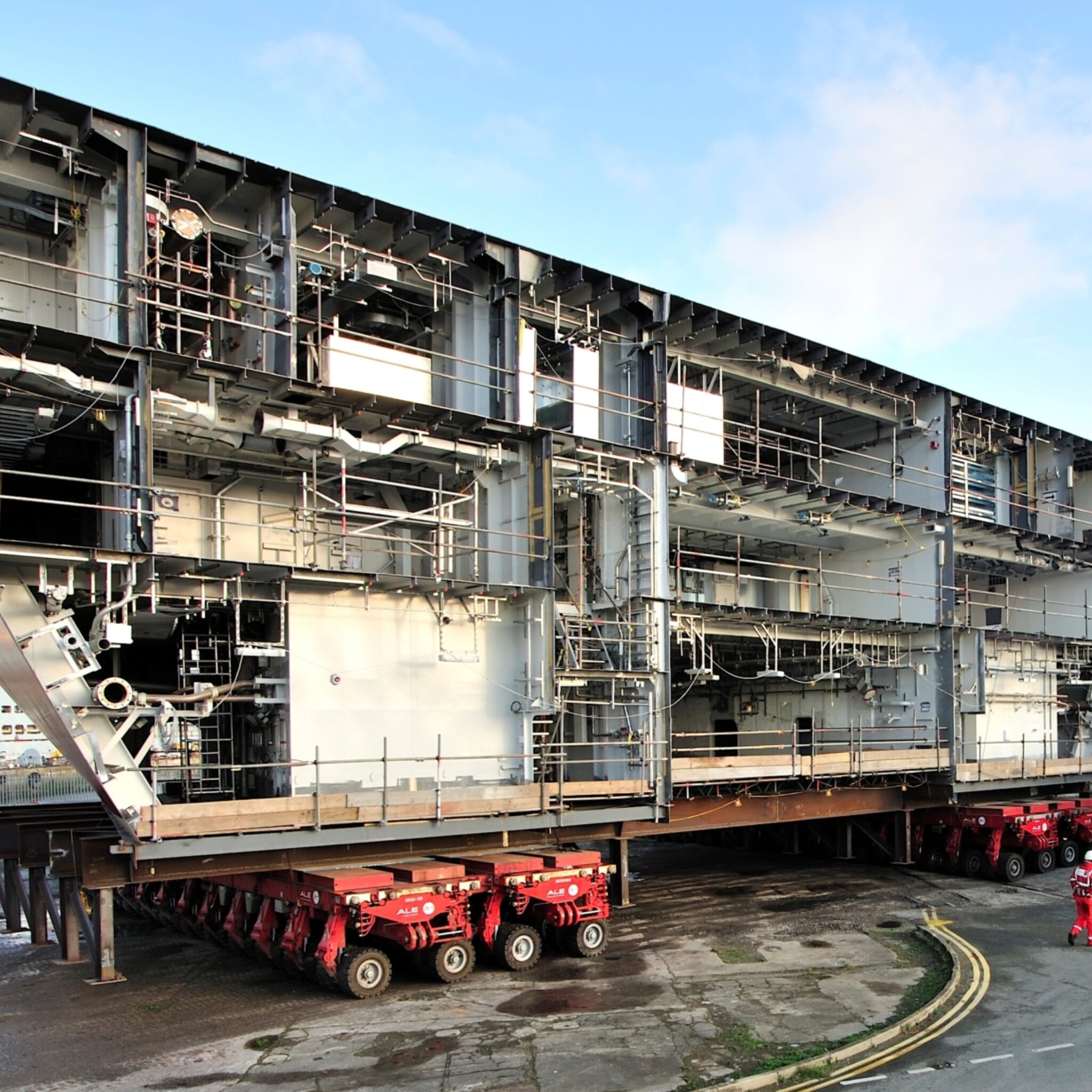